The installation of metal structures in marine environments is a critical aspect of industries such as shipbuilding, offshore oil and gas production, coastal infrastructure development, and renewable energy projects. The marine climate, characterized by high humidity, salt-laden air, aggressive environmental conditions, and strong winds, imposes unique challenges on the design, material selection, and installation processes of these structures. Companies like Ghaima Group specialize in addressing these challenges, ensuring that every aspect—from material selection to final installation—is optimized for durability, stability, and safety. This article explores the specific requirements and best practices, as exemplified by Ghaima Group, for ensuring the long-term performance of metal structures in such harsh environments.
Challenges of the Marine Climate
Metal structures in marine environments are subject to a combination of factors that can significantly impact their performance and longevity. Understanding these challenges is crucial for effective design and installation.
High Humidity
In marine environments, humidity levels are generally higher than in inland areas. The constant presence of moisture accelerates the corrosion process, particularly for metals like steel, which are prone to rusting. This corrosion is a result of electrochemical reactions between the metal and the oxygen in the air, facilitated by the presence of water. High humidity also promotes the growth of mold and mildew on surfaces, which can further degrade materials over time.
Salty Air
The presence of salts, particularly sodium chloride, in the air near coastal areas is a significant contributor to corrosion. Salt particles can adhere to the surfaces of metal structures, where they attract moisture, leading to the formation of a saline solution that accelerates the electrochemical reactions responsible for corrosion. This process, known as salt spray corrosion, is particularly aggressive and can rapidly degrade metal surfaces, leading to pitting and other forms of localized damage.
Strong Winds
Coastal and offshore areas are often subjected to strong winds, which can exert substantial horizontal and vertical loads on metal structures. These wind forces, combined with the abrasive action of salt and sand carried by the wind, can lead to material fatigue, erosion, and eventual structural failure if not properly accounted for in the design. Additionally, strong winds can complicate the installation process, making it difficult to position and secure components safely and accurately.
Aggressive Environment
The marine environment is inherently aggressive, with a combination of factors such as fluctuating temperatures, UV radiation, and exposure to seawater contributing to the degradation of metal structures. Seawater contains various corrosive elements, including chlorides, sulfates, and biological organisms, which can accelerate the deterioration of materials. This environment demands that all aspects of metal structure installation, from material selection to final assembly, be carefully planned and executed to mitigate these risks.
Materials and Coatings for Corrosion Protection
Given the harsh conditions of the marine environment, selecting the right materials and protective coatings is essential for ensuring the longevity and performance of metal structures.
Stainless Steel
Stainless steel is widely regarded as an ideal material for marine environments due to its high resistance to corrosion. The presence of chromium in stainless steel creates a passive oxide layer on the surface, which protects the metal from further oxidation. For marine applications, grades such as 316 and 316L are commonly used because of their enhanced resistance to pitting and crevice corrosion, which are common in saline conditions. While stainless steel is more expensive than other metals, its durability and low maintenance requirements make it a cost-effective choice for long-term applications.
Aluminum
Aluminum is another material that performs exceptionally well in marine environments. It forms a natural oxide layer that protects the metal from corrosion. Aluminum’s lightweight properties, combined with its strength and corrosion resistance, make it a popular choice for structures where weight is a critical factor, such as in shipbuilding and offshore platforms. However, aluminum can suffer from galvanic corrosion when in contact with more noble metals like copper or stainless steel, so careful consideration must be given to material compatibility.
Zinc and Zinc Coatings
Zinc is often used as a sacrificial anode to protect steel structures from corrosion through a process called galvanization. In this process, a layer of zinc is applied to steel, which then corrodes in preference to the underlying metal, thereby protecting it from rust. Zinc coatings can be applied through hot-dip galvanizing or electroplating, and the thickness of the coating is critical to the longevity of the protection. This method is widely used for structural steel components exposed to marine environments.
Epoxy and Polyurethane Coatings
Epoxy and polyurethane coatings provide a robust protective barrier against the corrosive effects of the marine environment. Epoxy coatings are particularly effective because they adhere strongly to metal surfaces and cure to form a hard, chemically resistant layer. Polyurethane coatings, often used as a topcoat, offer additional protection against UV radiation and mechanical wear. These coatings are essential for protecting structural steel, pipelines, and other critical components from corrosion and mechanical damage.
Design Considerations for Metal Structures in Marine Environments
Designing metal structures for marine environments requires a thorough understanding of the challenges posed by the climate and the selection of appropriate materials and protective measures.
Structural Design and Load Considerations
Marine structures must be designed to withstand both static and dynamic loads. Static loads include the weight of the structure itself and any equipment it supports, while dynamic loads are imposed by wind, waves, and, in some cases, seismic activity. The design must account for fatigue loading due to the constant motion of water and wind, which can cause cyclic stresses that lead to material fatigue over time. Advanced design tools such as finite element analysis (FEA) are often used to simulate these conditions and optimize the structural design.
Corrosion Allowances and Protective Measures
Incorporating corrosion allowances into the design is a common practice in marine environments. This involves deliberately oversizing certain components to compensate for the anticipated material loss due to corrosion over the structure’s service life. Additionally, the design may include features such as sacrificial anodes, cathodic protection systems, and the strategic placement of inspection and maintenance access points to facilitate regular upkeep.
Material Selection and Compatibility
The choice of materials for metal structures in marine environments is crucial. In addition to selecting corrosion-resistant materials like stainless steel and aluminum, it is essential to consider the compatibility of different metals to prevent galvanic corrosion. This type of corrosion occurs when two dissimilar metals are in contact in the presence of an electrolyte, such as seawater, leading to the accelerated corrosion of the less noble metal.
Protective Coatings and Surface Treatments
Applying protective coatings is a key strategy for extending the life of metal structures in marine environments. These coatings must be carefully selected based on the specific conditions the structure will face, such as exposure to salt spray, UV radiation, and mechanical wear. In addition to epoxy and polyurethane coatings, other treatments such as anodizing (for aluminum) and powder coating may be used to enhance corrosion resistance and surface durability.
Assembly and Installation in the Marine Environment
The installation of metal structures in marine environments involves specific challenges that must be addressed to ensure the safety and quality of the work.
Planning and Pre-Installation Considerations
Before installation begins, a comprehensive site assessment is necessary to understand the environmental conditions, including wind patterns, wave heights, tidal ranges, and the potential for extreme weather events. This information is used to develop a detailed installation plan that includes the timing of work, the selection of appropriate equipment, and the necessary safety measures. Pre-fabrication of components in controlled environments is often preferred, as it allows for better quality control and reduces the time spent on-site.
Handling Strong Winds and Waves
Strong winds and waves can pose significant challenges during the installation process. It is crucial to monitor weather conditions continuously and have contingency plans in place for sudden changes. During installation, temporary supports and guy lines may be used to stabilize structures against wind loads. In offshore installations, wave conditions must be carefully monitored, and installation work should ideally be scheduled during periods of calm seas.
Special Equipment and Safety Measures
The installation of metal structures in marine environments requires specialized equipment designed to withstand harsh conditions. This includes corrosion-resistant tools, lifting mechanisms, and fasteners. Safety is a top priority, and workers must be equipped with appropriate personal protective equipment (PPE), including life jackets, harnesses, and weather-resistant clothing. Safety protocols should include regular drills for emergency situations, such as man-overboard scenarios or equipment failure.
Qualified Personnel and Training
Given the complexities of installing metal structures in marine environments, it is essential that the work be carried out by highly qualified personnel with experience in similar conditions. Workers must be trained not only in the technical aspects of installation but also in safety procedures specific to the marine environment. This includes training in the use of specialized equipment, emergency response, and the recognition and mitigation of environmental hazards.
Maintenance and Long-Term Considerations
Once installed, metal structures in marine environments require ongoing maintenance to ensure their longevity and safety.
Regular Inspections and Monitoring
Regular inspections are essential for detecting early signs of corrosion, fatigue, or other structural issues. These inspections should be conducted both visually and using advanced techniques such as ultrasonic testing, radiography, and corrosion monitoring systems. Underwater inspections may involve divers or remotely operated vehicles (ROVs), particularly for submerged structures such as pipelines and offshore platforms.
Preventive Maintenance and Repairs
Preventive maintenance is crucial in extending the life of metal structures in marine environments. This includes regular cleaning to remove salt deposits, reapplication of protective coatings, and the replacement of sacrificial anodes. In some cases, more extensive repairs may be necessary, such as the replacement of corroded components or the reinforcement of areas subject to high stress.
Adaptation to Environmental Changes
Marine environments are dynamic and can change over time due to factors such as climate change, sea-level rise, and changes in wave patterns. Metal structures must be designed with the flexibility to adapt to these changes. For example, rising sea levels may require the elevation of coastal structures or the reinforcement of foundations. Similarly, increasing storm intensity may necessitate upgrades to structural components to withstand higher wind and wave loads.
Conclusion
The installation of metal structures in marine environments presents significant challenges that require a specialized approach to ensure the durability, stability, and safety of these structures. The harsh conditions of the marine climate demand careful consideration at every stage, from design and material selection to installation and long-term maintenance.
By employing corrosion-resistant materials such as stainless steel and aluminum, applying advanced protective coatings, and utilizing sophisticated design and installation techniques, it is possible to create metal structures that can withstand the harsh conditions of marine environments for decades. Additionally, the expertise of qualified personnel and the implementation of rigorous safety measures are critical to the success of these projects.
For industries operating in marine environments, such as shipbuilding, offshore oil and gas production, and coastal infrastructure development, the investment in specialized approaches to metal structure installation is essential. Companies like Ghaima Group, with extensive experience in these challenging environments, offer the expertise and reliability needed to ensure that metal structures perform effectively and safely in the most demanding conditions. By partnering with professionals, you can trust that your marine installations will meet the highest standards of quality and durability.
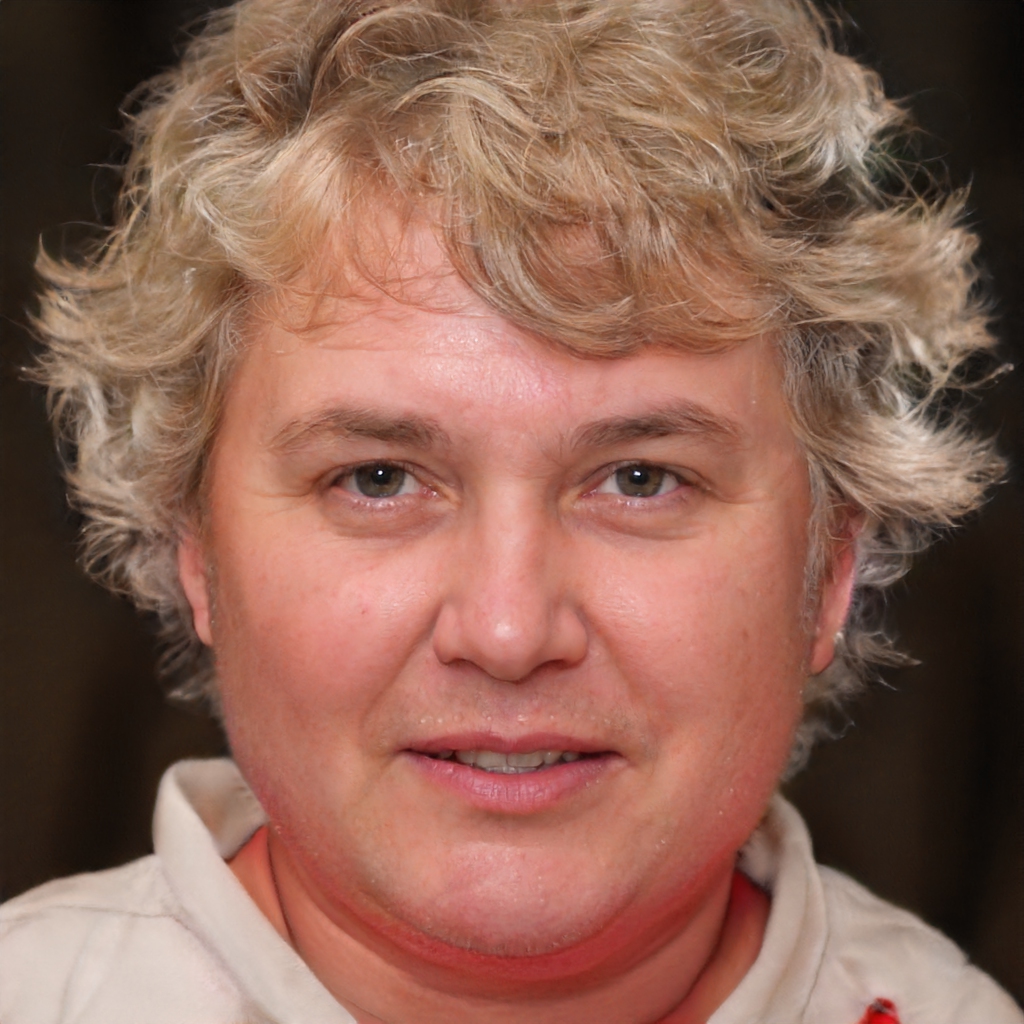
Surfer, dreamer, record lover, Vignelli fan and growthhacker. Making at the sweet spot between simplicity and mathematics to create strong, lasting and remarkable design. German award-winning designer raised in Austria & currently living in New York City.
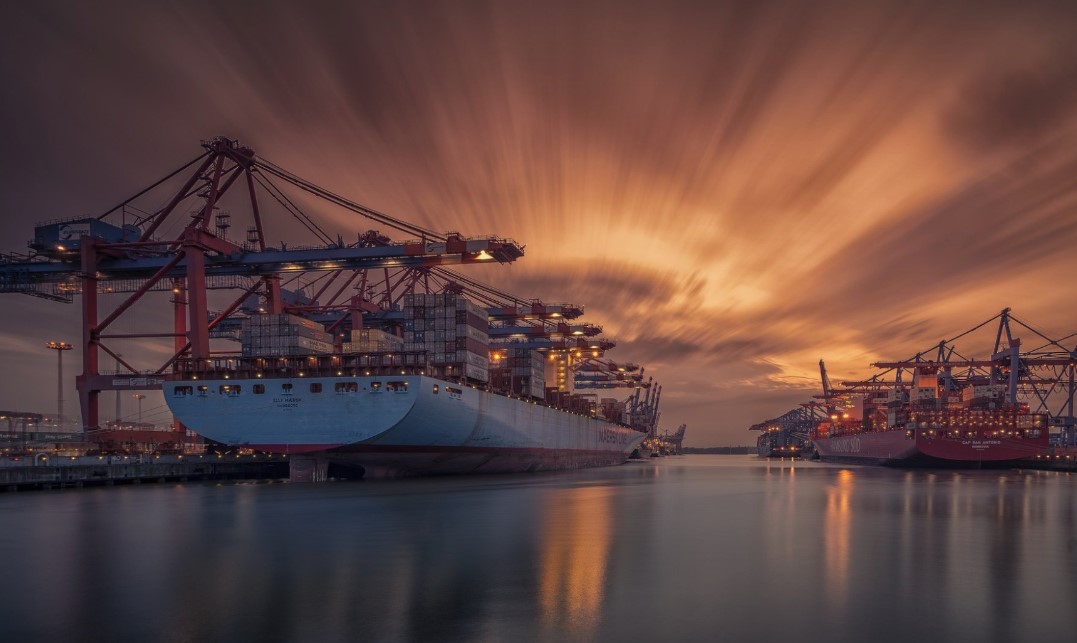